COPA-DATA is a partner in the “DIMA” project
The software specialist COPA-DATA is collaborating, as one of the first providers of a process control system, in the “DIMA – Decentralized Intelligence for Modular Applications” project, initiated by WAGO. The objective is to create a de-facto standard for decentralized, modular automation of process equipment and efficient engineering. This provides industrial companies with the possibility to implement process equipment in a flexible way and thus individualize their production.
Fluctuating procurement and sales markets, flexible relocation of production sites and the increasing requirement for customer-specific individualization of a product range are leading to ever-shorter product and innovation cycles in the process industry. Conventionally-constructed process technology equipment in the areas of chemical processing, food and beverages, cosmetics and pharmaceuticals are usually not flexible enough and cannot efficiently master the introduction of new products or amended production quantities.
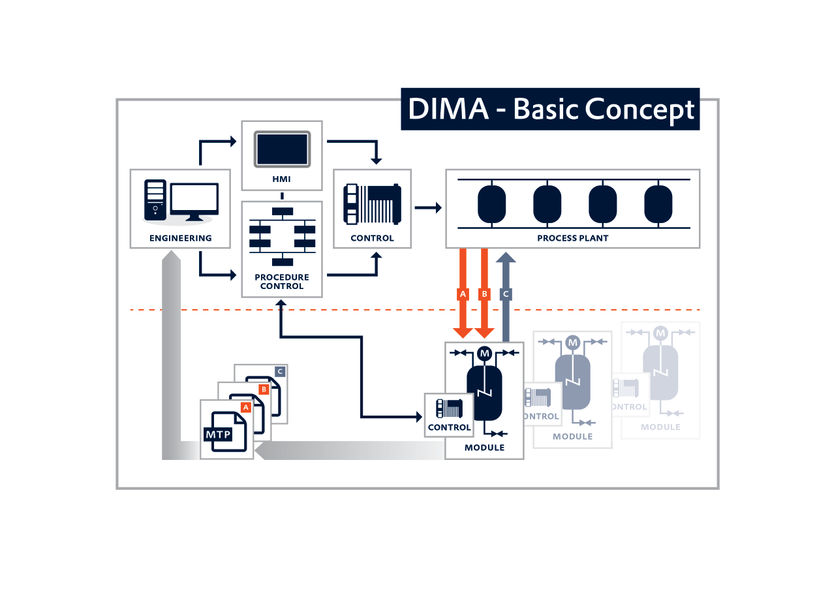
DIMA Basis Concept
WAGO Kontakttechnik GmbH & Co. KG
Individualization of process plants
WAGO, a global provider of electrical connection and automation systems, has therefore initiated the “DIMA – Decentralized Intelligence for Modular Applications” project. It meets the demand for individualization of process equipment and a high degree of modularity in the automation of production processes.
“Our aim is to considerably shorten the time between product approval and market availability. We estimate that 60 percent of the development time of process equipment can be saved. But this can only happen if the equipment is created in a modular manner and we give the company the possibility to act more quickly and flexibly”, explains Ulrich Hempen, Manager of Industry & Process Market Management at WAGO Kontakttechnik GmbH & Co. KG.
The committees of the User Association of Automation Technology in Process Industries (NAMUR) and the German Electrical and Electronic Manufacturers' Association (ZVEI) have taken on the DIMA approach and further specified it. The objective of the cooperation is the development of an international standard.
Service-orientated architecture
The idea of the DIMA concept is to compile an entire plant consisting of several autonomous equipment modules. An equipment module displays one or more standardized process steps, carries out procedures, operations or functions and thus provides a so-called service. A module provides its process-technology function as a service to the higher-level process control system, zenon – it takes on the role of a service provider. The process control system can call up the service offered by the module – it acts as a service user. DIMA consequently uses the paradigm of service-orientated architecture (SOA). The modules have their own “intelligence” in the DIMA concept. Each module is equipped with its own WAGO controller, which executes services and monitors the module status. If companies wish to amend a production process, they only need to exchange one or more modules. The production quantity can be increased by means of numbering-up, i.e. adding modules of the same type.
“The major advantage of modularization of equipment is the reduction of engineering work for the operator, both for commissioning and when making changes to the equipment. The operator can plan and construct modular equipment more efficiently, because a large part of the engineering can already take place in the module engineering phase. The modules then only need to be integrated into zenon”, explains Philipp Schmidt, Branch Office Manager at COPA-DATA Germany.
Electronic description model: Module Type Package
The technical implementation of the DIMA method requires a new definition for the description of process equipment modules: the “Module Type Package” (MTP). The following information is stored in this MTP: communication parameters for easy integration of the module into the equipment; services, i.e. the description of the process performance characteristics of the module, as well as graphics information for operation and observation. In addition, there are further descriptions, such as information on status, diagnosis, history and archiving.
Handling and management of the modules
In order to design the complete engineering or re-engineering process as efficiently as possible, COPA-DATA has developed an MTP handling and management system. With this system, companies can read in the MTPs, create all required variables and operating screens, and define their connection. All information with regard to name, size, position and variable connection of the screen objects in the operating screens come from the MTP. This guarantees that the operating screens of modules of different manufacturers, which are read in by different MTPs, correspond to the customer-specific look and feel in the control system. Users can also track, at any time, which artifacts in zenon have been created by which MTP. This allows the connection of the different modules required in the process, even during ongoing operation. zenon also gives customers the possibility to select and export customized services and operating screens. This way, companies can set out a concept for reuse and reduce project-related costs. In addition to the creation and connection of variables and operating screens, the services that are also included in the MTP are created as phases in the zenon Batch Control module. The parameters of the phases can be set as required and linked to one another in the form of recipes. The production process of the equipment can begin after this step. If necessary, cross-module interlockings can be implemented in zenon using the variables created, and additional messages can be set up.